“Producing leather” means transforming animal skin into leather articles such as car interior, upholstered furniture, bags/accessories or shoes. Tanning is hence a process that modifies the protein structure of skin and makes it durable. Appropriate chemical auxiliaries are needed for the industrial processing of the raw material, the animal hide.
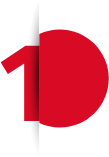
The production process starts with the elimination of dirt, hair and, subsequently, the removal of fat and residual tissues. The skin is then divided into two or more layers, in order to reduce its thickness (heavy or very light and almost impalpable garments). For these production steps, so called Beam House Chemicals are used.
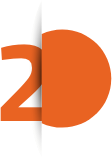
The leather production process continues with deliming and soaking with enzymes, to improve the quality of the leather and to make it soft and pleasant to wear.
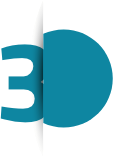
Surfactants eliminate most of the fat and uniform its distribution throughout the skin.

Tanning agents bind to the skin and ensure the persistence over time of the achieved consistency.
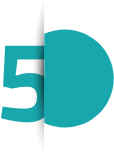
Dyeing agents may be used if needed, to have a coloured leather product.
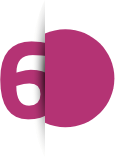
Fatliquoring agents are used due to the fact that the natural fat had to be removed in the beginning (as it would become rancid) and thus the leather has to receive some regreasement: fatliquoring means reapplying water-soluble oils to leather.
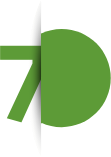
In order to receive certain effects in the surface, finishing agents can be applied – e. g. for achieving waterproof leather, to preserve old and dry leather by softening, to achieve a special patina or a glossy, silky or rough appearance on the final article and so on.